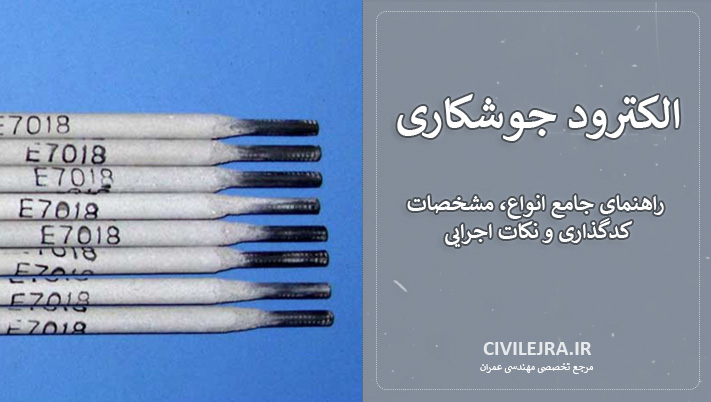
الکترودهای جوشکاری : جوشکاری، هنری صنعتی و فرآیندی بنیادین در دنیای مهندسی و ساختوساز است که نقشی حیاتی در اتصال دائمی قطعات فلزی ایفا میکند. از سازههای عظیم فولادی گرفته تا ریزترین قطعات الکترونیکی، جوشکاری در قلب پیشرفتهای تکنولوژیکی قرار دارد. در این میان، الکترود جوشکاری به عنوان یکی از مهمترین و تأثیرگذارترین اجزا، تعیینکننده کیفیت، استحکام و طول عمر اتصال جوشی است. انتخاب صحیح الکترود، در کنار مهارت جوشکار و تنظیمات دستگاه، جوشی ایمن، پایدار و با خواص مکانیکی مطلوب را تضمین میکند.
این راهنمای جامع به منظور ارائه یک دیدگاه کامل و عمیق در مورد الکترودهای جوشکاری، انواع آنها، مشخصات فنی، سیستمهای کدگذاری، کاربردهای خاص، و نکات حیاتی در انتخاب و نگهداری آنها تدوین شده است. هدف ما این است که شما را با تمام جنبههای مرتبط با این جزء کلیدی جوشکاری آشنا کنیم تا بتوانید با اطمینان خاطر، بهترین انتخاب را برای نیازهای پروژههای خود داشته باشید.
الکترود جوشکاری چیست؟ شناخت ساختار و عملکرد
در سادهترین تعریف، الکترود جوشکاری یک میله فلزی قابل ذوب (هسته) است که با یک پوشش شیمیایی خاص به نام فلاکس (Flux) احاطه شده است. این ساختار دوگانه، فرآیند جوشکاری با قوس الکتریکی دستی (SMAW) یا “جوشکاری با الکترود روکشدار” را امکانپذیر میسازد.
هسته فلزی (Core Wire): هسته الکترود معمولاً از جنسی مشابه یا سازگار با فلز پایه (Metal Base) ساخته میشود. این هسته ذوب شده و به عنوان فلز پرکننده (Filler Metal) عمل میکند و بین دو قطعه فلزی ذوبشده، اتصال ایجاد میکند. جنس هسته میتواند از فولاد کربن، فولاد آلیاژی، فولاد ضد زنگ، نیکل، مس، آلومینیوم و سایر آلیاژها باشد.
پوشش فلاکس (Flux Coating): این روکش، که به دقت فرموله شده است، وظایف چندگانهای را بر عهده دارد که همگی برای یک جوش موفق حیاتی هستند:
- تولید گاز محافظ (Shielding Gas): در اثر حرارت قوس، فلاکس تجزیه شده و گازهای مختلفی (مانند دیاکسید کربن، مونوکسید کربن، هیدروژن و بخار آب) را آزاد میکند. این گازها یک پوشش محافظ در اطراف حوضچه مذاب و انتهای الکترود ایجاد کرده و از تماس اکسیژن و نیتروژن هوا با فلز مذاب جلوگیری میکنند. تماس با این گازها میتواند منجر به اکسیداسیون، تخلخل (Porosity) و کاهش خواص مکانیکی جوش شود.
- تشکیل سرباره (Slag Formation): پس از ذوب شدن، مواد موجود در فلاکس لایهای از سرباره مایع را روی حوضچه مذاب تشکیل میدهند. این سرباره پس از سرد شدن، سخت شده و از جوش در حال انجماد در برابر اکسیداسیون و سرد شدن سریع محافظت میکند. سرباره همچنین به شکلگیری منظم و صاف مهره جوش (Weld Bead) کمک میکند و ناخالصیها را جذب میکند. پس از سرد شدن کامل، سرباره به راحتی قابل جدا شدن است.
- پایداری قوس الکتریکی (Arc Stabilization): فلاکس حاوی عناصری است که به یونیزاسیون گازها در قوس کمک کرده و پایداری قوس را افزایش میدهند. این امر باعث میشود که قوس به صورت یکنواخت و پایدار بسوزد و جوشکار بتواند کنترل بهتری بر فرآیند داشته باشد.
- افزودن عناصر آلیاژی (Alloying Elements): برخی از فلاکسها حاوی عناصری مانند منگنز، سیلیسیوم، نیکل، کروم و مولیبدن هستند. این عناصر به حوضچه مذاب اضافه شده و خواص مکانیکی جوش (مانند استحکام کششی، چقرمگی، مقاومت به خوردگی) را بهبود میبخشند.
- کاهش ناخالصیها (Deoxidation): فلاکس میتواند حاوی مواد احیاکننده باشد که اکسیژن و سایر ناخالصیها را از فلز مذاب حذف کرده و به این ترتیب از ایجاد تخلخل و اکسیداسیون داخلی در جوش جلوگیری میکند.
طبقهبندی الکترودهای جوشکاری: انواع و ویژگیها
الکترودهای جوشکاری بر اساس جنس هسته، نوع روکش و کاربردشان به دستههای اصلی تقسیم میشوند. آشنایی با این دستهبندیها برای انتخاب صحیح الکترود ضروری است.
۱. الکترودهای فولاد کربن و فولادهای کمآلیاژ (Carbon Steel & Low-Alloy Steel Electrodes)
این دسته پرکاربردترین الکترودها در صنعت هستند و بر اساس نوع پوشش فلاکس به زیرگروههای اصلی تقسیم میشوند:
-
الکترودهای با روکش سلولزی (Cellulosic Electrodes – AWS E6010, E6011):
- ترکیب روکش: دارای درصد بالایی از سلولز (معمولاً ۱۵-۳۰%) که در اثر سوختن، حجم زیادی گاز محافظ (عمدتاً هیدروژن و مونوکسید کربن) تولید میکند.
- ویژگیها:
- نفوذ عمیق (Deep Penetration): به دلیل فشار بالای قوس و حوضچه مذاب داغ، نفوذ بسیار عمیقی در فلز پایه ایجاد میکنند.
- سرعت بالا: امکان جوشکاری با سرعت بالا را فراهم میکنند.
- حساسیت کم به آلایندگی: میتوانند روی سطوح کمی زنگزده، رنگزده یا کثیف نیز عملکرد قابل قبولی داشته باشند.
- موقعیت جوشکاری: عالی برای تمام موقعیتها، به ویژه موقعیت عمودی رو به پایین (Vertical Down).
- ظاهر جوش: مهره جوش خشنتر و سرباره ناپیوسته که نیاز به تمیزکاری بیشتری دارد.
- انتقال فلز: اسپری خشن و پر سر و صدا.
- هیدروژن: سطح هیدروژن بالا در جوش، که ممکن است خطر ترکخوردگی هیدروژنی را افزایش دهد، به خصوص در فولادهای پرکربن یا آلیاژی.
- کاربردها: جوشکاری خطوط لوله (به ویژه پاس ریشه)، مخازن ذخیره، ساختوساز عمومی، کارهایی که نیاز به نفوذ بالا و سرعت دارند.
- جریان: E6010 فقط DC+ (قطبیت معکوس)، E6011 هم AC و هم DC+ (مناسب برای دستگاههای AC خانگی).
-
الکترودهای با روکش رتیلی (Rutile Electrodes – AWS E6013, E7014):
- ترکیب روکش: حاوی مقادیر زیادی دیاکسید تیتانیوم (روتایل).
- ویژگیها:
- قوس پایدار و نرم: شروع قوس آسان و جوشکاری روان، حتی برای جوشکاران مبتدی.
- ظاهر جوش زیبا: مهره جوش صاف، یکنواخت و با ظاهر عالی.
- سرباره آسانجداشونده: سرباره خودبهخود یا با کمترین تلاش جدا میشود.
- نفوذ کم تا متوسط: برای جوشکاری فلزات نازک و متوسط مناسب هستند.
- اسپاتر کم (Low Spatter): پاشش کمتری دارند.
- کاربردها: کارهای عمومی، جوشکاری ورقهای نازک، ساخت مبلمان فلزی، مصارف خانگی، جوشکاری فولادهای کربن پایین.
- جریان: AC و DC (هم قطبیت مستقیم و هم معکوس).
- نکات: برای سازههای تحت بار دینامیکی یا جوشکاری فولادهای آلیاژی که نیاز به خواص مکانیکی بالا دارند، توصیه نمیشوند.
-
الکترودهای با روکش قلیایی/کمهیدروژن (Low Hydrogen / Basic Electrodes – AWS E7018, E7016, E7015):
- ترکیب روکش: دارای درصد بالایی از کربناتها (کربنات کلسیم، منیزیم) و فلورایدها. رطوبت بسیار کمی دارند.
- ویژگیها:
- خواص مکانیکی عالی: جوش با استحکام کششی بالا، چقرمگی (Toughness) عالی در دماهای پایین، و مقاومت فوقالعاده در برابر ترکخوردگی (به دلیل محتوای هیدروژن بسیار پایین).
- نفوذ متوسط: قابلیت کنترل خوب بر حوضچه مذاب.
- ایمنی جوش: به دلیل کاهش خطر ترکخوردگی هیدروژنی، برای جوشکاری فولادهای پرکربن، فولادهای آلیاژی، و سازههای تحت بار سنگین ایدهآل هستند.
- موقعیت جوشکاری: عمدتاً برای موقعیتهای تخت، افقی، عمودی رو به بالا و سقفی مناسب هستند.
- سرباره: سرباره سنگین و کمی دشوارتر برای جدا شدن نسبت به الکترودهای رتیلی.
- کاربردها: ساخت پلها، کشتیسازی، دیگهای بخار، لولهکشی فشار بالا، سازههای نیروگاه، جوشکاری تعمیراتی قطعات حساس.
- جریان: E7018 عمدتاً DC+ (قطبیت معکوس) و برخی انواع برای AC نیز مناسب هستند. E7016 برای AC و DC، E7015 فقط برای DC+.
- نکات مهم: حساسیت شدید به رطوبت. باید در بستهبندی پلمپ شده و در کوره خشککن نگهداری شوند. رطوبت باعث افزایش هیدروژن در جوش و خطر ترکخوردگی میشود.
۲. الکترودهای فولاد ضد زنگ (Stainless Steel Electrodes)
این الکترودها برای جوشکاری فولادهای ضد زنگ با ترکیب شیمیایی متنوع طراحی شدهاند و مقاومت به خوردگی و خواص مکانیکی فلز پایه را حفظ میکنند.
- کدگذاری: معمولاً با E3XX-XX شناخته میشوند (مثال: E308L-16، E316L-16). رقم سه رقمی اول نشاندهنده نوع فولاد ضد زنگ (سری ۳۰۰، ۴۰۰ و …)، و L یا H نشاندهنده درصد کربن (L برای کربن کم Low Carbon و H برای کربن بالا High Carbon) است. دو رقم آخر نیز مشابه الکترودهای فولادی، موقعیت و نوع روکش را نشان میدهند.
- انواع متداول:
- E308L: برای جوشکاری فولادهای ضد زنگ آستنیتی مانند ۳۰۴ و 304L. “L” نشاندهنده کربن پایین برای جلوگیری از خوردگی بیندانهای.
- E316L: برای جوشکاری فولادهای ضد زنگ آستنیتی حاوی مولیبدن مانند ۳۱۶ و 316L، که مقاومت به خوردگی در محیطهای حاوی کلر را بهبود میبخشد.
- E309: برای جوشکاری فولاد ضد زنگ به فولاد کربن یا برای لایهگذاری (Cladding) روی فولاد کربن.
- ویژگیها: مقاومت عالی در برابر خوردگی، خواص مکانیکی خوب در دماهای بالا، و ظاهر جوش مطلوب.
- کاربردها: صنایع غذایی، شیمیایی، داروسازی، نفت و گاز، پتروشیمی، و کاربردهایی که نیاز به مقاومت به خوردگی بالا دارند.
- نکات: نیاز به کنترل دمای بینپاسی برای جلوگیری از ترکخوردگی و اعوجاج.
۳. الکترودهای چدن (Cast Iron Electrodes)
جوشکاری چدن به دلیل ماهیت شکننده آن دشوار است. این الکترودها برای ترمیم و اتصال قطعات چدنی فرموله شدهاند.
- کدگذاری: معمولاً با ENi-CI (هسته نیکل خالص) یا ENiFe-CI (هسته نیکل-آهن) شناخته میشوند.
- ویژگیها:
- ENi-CI: نرمتر، قابلیت ماشینکاری جوش بالا، مناسب برای ترمیم ترکها و شکستگیهای جزئی.
- ENiFe-CI: قویتر، مقاومت به ترکخوردگی بهتر در جوشکاری قطعات سنگینتر.
- کاربردها: تعمیر بلوک موتور، سرسیلندر، پمپها، محفظههای گیربکس و سایر قطعات چدنی شکسته یا فرسوده.
- نکات: پیشگرمایش و پسگرمایش قطعات چدنی برای کاهش تنش و جلوگیری از ترکخوردگی بسیار مهم است.
۴. الکترودهای آلومینیوم (Aluminum Electrodes)
- کدگذاری: معمولاً با E4043 یا E1100.
- ویژگیها: برای جوشکاری آلومینیوم و آلیاژهای آن. نفوذ خوب و پایداری قوس.
- کاربردها: ساخت و تعمیر قطعات آلومینیومی که روشهای جوشکاری TIG یا MIG برای آنها مناسب نیستند.
- نکات: آلومینیوم به سرعت اکسید میشود و نقطه ذوب پایینی دارد، که جوشکاری آن را چالشبرانگیز میکند. الکترودها باید کاملاً خشک باشند.
۵. الکترودهای سختکاری (Hardfacing Electrodes)
- هدف: ایجاد یک لایه مقاوم در برابر سایش، خوردگی یا ضربه بر روی سطح قطعات فلزی.
- ترکیب: حاوی عناصر آلیاژی مانند کروم، مولیبدن، تنگستن و کربن بالا.
- کاربردها: افزایش طول عمر قطعات در معرض سایش شدید مانند تیغههای بولدوزر، لبههای سطل، چرخدندهها و ابزار کشاورزی.
سیستم کدگذاری الکترودها (AWS A5.1 و A5.5)
استاندارد AWS (انجمن جوشکاری آمریکا) یک سیستم کدگذاری جهانی را برای الکترودهای جوشکاری SMAW ارائه میدهد که به جوشکاران و مهندسان امکان میدهد به سرعت مشخصات کلیدی یک الکترود را شناسایی کنند. برای الکترودهای فولاد کربن و کمآلیاژ، رایجترین استاندارد AWS A5.1 است، در حالی که برای الکترودهای کمآلیاژ با خواص خاص، از AWS A5.5 استفاده میشود.
بیایید یک مثال رایج را بررسی کنیم: E7018
- E: نشاندهنده “الکترود” (Electrode).
- دو رقم اول (۷۰): این دو رقم، حداقل استحکام کششی نهایی فلز جوش بر حسب هزار پوند بر اینچ مربع (KSI) را نشان میدهند.
- در این مثال، ۷۰ به معنای ۷۰,۰۰۰ پوند بر اینچ مربع (psi) یا حدود ۴۸۲ مگاپاسکال (MPa) است.
- این عدد معمولاً بین ۶۰ (۶۰,۰۰۰ psi) تا ۱۲۰ (۱۲۰,۰۰۰ psi) متغیر است.
- رقم سوم (۱): این رقم، موقعیتهای جوشکاری را که الکترود میتواند در آن استفاده شود، مشخص میکند:
- ۱: تمام موقعیتها (All Positions): تخت (Flat), افقی (Horizontal), عمودی (Vertical), و سقفی (Overhead). (مانند E6010, E6011, E6013, E7018)
- ۲: فقط موقعیتهای تخت و افقی (Flat and Horizontal Positions). (مانند E7024)
- ۴: تمام موقعیتها، اما به ویژه برای جوشکاری عمودی رو به پایین (Vertical Down) مناسب است. (مانند E7048)
- رقم چهارم (۸): این رقم اطلاعات کلیدی در مورد نوع روکش الکترود، نوع جریان جوشکاری (AC/DC) و عمق نفوذ قوس را ارائه میدهد:
- ۰: روکش سلولزی-سدیم، جریان DC+ (قطبیت معکوس)، نفوذ عمیق (مثال: E6010).
- ۱: روکش سلولزی-پتاسیم، جریان AC یا DC+، نفوذ عمیق (مثال: E6011).
- ۲: روکش رتیل-سدیم، جریان AC یا DC- (قطبیت مستقیم)، نفوذ متوسط (مثال: E6012).
- ۳: روکش رتیل-پتاسیم، جریان AC یا DC، نفوذ متوسط (مثال: E6013).
- ۴: روکش رتیل-پودر آهن، جریان AC یا DC، نفوذ متوسط تا بالا (مثال: E7014).
- ۵: روکش کم هیدروژن-سدیم، جریان DC+، نفوذ متوسط (مثال: E7015).
- ۶: روکش کم هیدروژن-پتاسیم، جریان AC یا DC+، نفوذ متوسط (مثال: E7016).
- ۷: روکش پودر آهن-اکسید آهن، جریان AC یا DC، نفوذ کم (مثال: E7017).
- ۸: روکش کم هیدروژن-پودر آهن، جریان AC یا DC+، نفوذ متوسط تا بالا (مثال: E7018).
پسوندهای اختیاری: برخی الکترودها دارای پسوندهای اضافی هستند که اطلاعات بیشتری درباره خواص شیمیایی یا مکانیکی خاص ارائه میدهند:
- -A1, -B1, -C1, etc.: نشاندهنده عناصر آلیاژی خاص (مثلاً -A1 برای مولیبدن، -B1 برای کروم-مولیبدن).
- -H4, -H8, -H16: حداکثر محتوای هیدروژن منتشر شونده در فلز جوش (به میلیلیتر در ۱۰۰ گرم فلز جوش)، که نشاندهنده قابلیت الکترود در کاهش خطر ترکخوردگی هیدروژنی است. الکترودهای کم هیدروژن عموماً دارای H4 یا H8 هستند.
- -R: نشاندهنده مقاومت بهتر به جذب رطوبت.
نکات کلیدی در انتخاب الکترود مناسب
انتخاب صحیح الکترود جوشکاری برای موفقیت یک پروژه جوشکاری حیاتی است. انتخاب اشتباه میتواند منجر به جوشی ضعیف، ترکخورده یا غیرقابل قبول شود. در اینجا عوامل مهمی که باید در نظر بگیرید، آورده شده است:
-
نوع فلز پایه (Base Metal):
- سازگاری شیمیایی: مهمترین فاکتور، اطمینان از این است که ترکیب شیمیایی الکترود با فلز پایه سازگار باشد تا یک اتصال متالورژیکی قوی و همگن ایجاد شود. به عنوان مثال، برای فولاد کربن، از الکترودهای فولاد کربن استفاده کنید؛ برای فولاد ضد زنگ، الکترودهای ضد زنگ مناسب را انتخاب کنید.
- خواص مکانیکی: الکترود باید خواص مکانیکی (مانند استحکام کششی، نقطه تسلیم، چقرمگی) مشابه یا بالاتر از فلز پایه را فراهم کند.
-
ضخامت فلز پایه:
- فلزات نازک: برای ورقهای نازک (کمتر از ۳ میلیمتر)، الکترودهایی با نفوذ کمتر (مانند E6013) که احتمال سوختگی (Burn-through) را کاهش میدهند، مناسبترند.
- فلزات ضخیم: برای قطعات ضخیمتر، الکترودهایی با نفوذ عمیقتر (مانند E6010) یا الکترودهایی که امکان جوشکاری با آمپراژ بالا را میدهند (مانند E7018) مناسبترند.
-
موقعیت جوشکاری (Welding Position):
- هر الکترود برای یک یا چند موقعیت جوشکاری خاص طراحی شده است (مثال: تمام موقعیتها، تخت، افقی، عمودی، سقفی). رقم سوم در کد AWS این مشخصه را نشان میدهد.
- الکترودهای “تمام موقعیت” انعطافپذیری بیشتری را ارائه میدهند.
-
خواص مکانیکی مورد نیاز جوش:
- استحکام کششی: آیا جوش باید بارهای کششی سنگین را تحمل کند؟ (به رقم اول در کد AWS توجه کنید).
- چقرمگی و مقاومت به ترکخوردگی: برای سازههای تحت بار دینامیکی، شوک یا دماهای پایین، الکترودهای کم هیدروژن (مانند E7018) که مقاومت عالی به ترکخوردگی دارند، ضروری هستند.
- مقاومت به خوردگی: در محیطهای خورنده، الکترودهای مناسب فولاد ضد زنگ یا آلیاژهای خاص مورد نیاز است.
- قابلیت ماشینکاری: در برخی کاربردها (مانند جوشکاری چدن)، قابلیت ماشینکاری جوش پس از اتمام کار مهم است.
-
نوع جریان جوشکاری (AC/DC):
- دستگاه جوش شما AC (جریان متناوب) است یا DC (جریان مستقیم)؟ برخی الکترودها فقط با یک نوع جریان کار میکنند، در حالی که برخی دیگر با هر دو سازگارند.
- DC+ (قطبیت معکوس): بیشترین نفوذ و نرخ رسوب بالا (برای E7018، E6010).
- DC- (قطبیت مستقیم): نفوذ کمتر، نرخ رسوب بالاتر، برای جوشکاری ورقهای نازک (برای E6012، برخی از E6013).
- AC: برای دستگاههای خانگی و ژنراتورهای قابل حمل، نفوذ متوسط.
-
شرایط سطح فلز پایه (Surface Condition):
- آیا فلز پایه تمیز است یا دارای زنگزدگی، رنگ یا آلودگی است؟ برخی الکترودها (مانند E6010, E6011) در برابر آلودگیهای سطح مقاومتر هستند، در حالی که الکترودهای کم هیدروژن نیاز به سطوح بسیار تمیز دارند.
-
محیط کار:
- در محیطهای مرطوب یا در فضای باز، خطر جذب رطوبت توسط الکترودها وجود دارد. استفاده از الکترودهای کم هیدروژن در این شرایط با نگهداری صحیح، اهمیت بیشتری پیدا میکند.
-
مهارت جوشکار:
- برخی الکترودها (مانند E6013) قوس نرم و پایداری دارند و برای جوشکاران مبتدی مناسبترند.
- الکترودهای کم هیدروژن (مانند E7018) نیاز به مهارت و تجربه بیشتری در کنترل قوس و حوضچه مذاب دارند.
نگهداری صحیح الکترودهای جوشکاری: تضمین کیفیت جوش
نگهداری نامناسب الکترودها میتواند به معنای هدر رفتن مواد و تلاش، و تولید جوشی معیوب باشد. رطوبت، دشمن اصلی الکترودها، به ویژه الکترودهای کم هیدروژن است.
-
خشک نگهداری:
- محیط نگهداری: الکترودها را همیشه در محیطی خشک، با دمای ثابت و دور از رطوبت، رطوبت نسبی بالا، نوسانات دما و میعان نگهداری کنید.
- بستهبندی پلمپشده: الکترودها باید تا زمان استفاده در بستهبندی اصلی و پلمپشده کارخانه نگهداری شوند. این بستهبندیها معمولاً ضد رطوبت هستند.
-
کوره خشککن (Baking Oven / Drying Oven):
- ضرورت برای الکترودهای کم هیدروژن: الکترودهای با روکش قلیایی/کم هیدروژن (مانند E7018) به شدت رطوبتگیر هستند. حتی مقدار کمی رطوبت میتواند باعث ایجاد حبابهای هیدروژن در جوش شده و منجر به ترکخوردگی تاخیری (Delayed Cracking) شود.
- دستورالعملهای تولیدکننده: همیشه الکترودهای کم هیدروژن را قبل از استفاده، طبق دستورالعمل تولیدکننده در کوره خشککن در دما و زمان مشخص (معمولاً ۲۵۰ تا ۴۵۰ درجه سانتیگراد برای چند ساعت) خشک کنید.
- جعبههای گرمکن (Quiver / Holding Oven): پس از خشک شدن در کوره اصلی، الکترودها باید در جعبههای گرمکن قابل حمل (Quiver) در محل کار نگهداری شوند که دما را در حدود ۷۰ تا ۱۵۰ درجه سانتیگراد حفظ میکنند تا از جذب مجدد رطوبت در طول فرآیند جوشکاری جلوگیری شود.
-
مدت زمان ماندگاری:
- حتی در شرایط نگهداری ایدهآل، الکترودها عمر مفیدی دارند. به تاریخ تولید و انقضا روی بستهبندی توجه کنید.
- الکترودهایی که بستهبندی آنها آسیب دیده یا برای مدت طولانی در معرض هوای آزاد بودهاند، باید دور ریخته شوند یا مجدداً خشک شوند (در صورت امکان و منطبق با استانداردها).
-
مدیریت موجودی:
- سیستم “اولین ورودی، اولین خروجی” (FIFO) را برای الکترودها رعایت کنید تا الکترودهای قدیمیتر ابتدا مصرف شوند.
چالشها و مسائل رایج مرتبط با الکترودها
- تخلخل (Porosity): وجود حبابهای گاز در جوش، که میتواند ناشی از رطوبت در الکترود، آلودگی سطح فلز پایه، یا سرعت جوشکاری نامناسب باشد.
- ترکخوردگی (Cracking):
- ترکخوردگی گرم (Hot Cracking): معمولاً در حین انجماد جوش رخ میدهد و به ترکیب شیمیایی فلز جوش و فلز پایه مرتبط است.
- ترکخوردگی سرد/هیدروژنی (Cold Cracking / Hydrogen Cracking): رایجترین نوع، ناشی از حضور هیدروژن در جوش، تنشهای پسماند و ساختار متالورژیکی حساس. استفاده از الکترودهای کم هیدروژن و پیشگرمایش/پسگرمایش از آن جلوگیری میکند.
- جوش نامنظم یا غیریکنواخت: میتواند ناشی از عدم پایداری قوس، تکنیک نامناسب جوشکاری، یا الکترود نامناسب باشد.
- مشکل در شروع قوس: ممکن است به دلیل رطوبت در الکترود، یا روکش آسیبدیده باشد.
- جدا نشدن سرباره: نشانه انتخاب الکترود نامناسب یا تنظیمات نادرست دستگاه.
آینده الکترودهای جوشکاری و تکنولوژیهای نوظهور
صنعت جوشکاری دائماً در حال تکامل است و الکترودهای جوشکاری نیز از این قاعده مستثنی نیستند. پیشرفتها در این زمینه شامل:
- افزایش بهرهوری: توسعه الکترودهایی با نرخ رسوب بالاتر و پاشش کمتر برای افزایش سرعت جوشکاری و کاهش ضایعات.
- کاهش انتشار دود و ذرات: تمرکز بر روی فرمولاسیونهای جدید فلاکس که میزان دود و ذرات معلق مضر را کاهش میدهند و محیط کار ایمنتری فراهم میکنند.
- خواص مکانیکی بهبود یافته: الکترودهایی با قابلیتهای پیشرفتهتر مانند مقاومت به خزش در دماهای بالا، مقاومت به سایش فوقالعاده و چقرمگی بالاتر در دماهای برودتی.
- تخصصگرایی بیشتر: تولید الکترودهای خاصتر برای آلیاژهای جدید و کاربردهای نوین در صنایعی مانند هوافضا و انرژیهای تجدیدپذیر.
- جوشکاری رباتیک و اتوماتیک: توسعه الکترودها و فرآیندهای مرتبط برای بهینهسازی جوشکاری خودکار و رباتیک، که نیاز به پایداری قوس بسیار بالا و تکرارپذیری دقیق دارند.
نتیجهگیری
الکترودهای جوشکاری، فراتر از یک “میله فلزی”، ابزاری پیچیده و مهندسیشده هستند که در قلب هر فرآیند جوشکاری موفقی قرار دارند. درک عمیق از انواع مختلف، سیستم کدگذاری، مشخصات فنی و نکات نگهداری آنها، برای هر جوشکار حرفهای، مهندس، یا حتی علاقهمند به جوشکاری ضروری است. انتخاب صحیح الکترود نه تنها کیفیت و استحکام جوش را تضمین میکند، بلکه به افزایش بهرهوری، کاهش هزینهها و تضمین ایمنی پروژه نیز کمک شایانی میکند.
همواره به یاد داشته باشید که مشورت با تولیدکنندگان، مطالعه دقیق کاتالوگها و رعایت استانداردهای بینالمللی مانند AWS، بهترین راه برای اطمینان از انتخاب الکترود مناسب برای هر کاربرد خاص است. با این دانش، میتوانید با اطمینان خاطر بیشتری قدم در دنیای جوشکاری بگذارید و اتصالات محکم و پایداری را خلق کنید.
آیا برای پروژه بعدی خود آمادهاید که بهترین الکترود را انتخاب کنید؟
اگر این راهنما برای شما مفید بود، پیشنهاد میکنیم سایر مقالات بخش «آموزشهای تخصصی و نکات اجرایی» سایت سیویل اجرا را مطالعه کنید و برای بهروزترین نکات فنی به کانال مهندسین عمران بپیوندید.
مطالب پیشنهادی :